Laser Power Monitoring Reduces Loss For This EV Battery Manufacturer
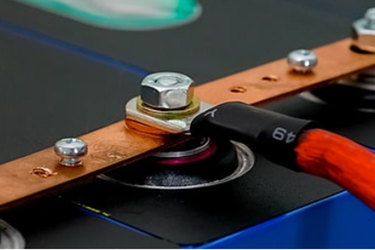
An electric vehicle battery manufacturer in the Republic of Korea was facing a critical challenge in their laser welding process. Each EV battery required over 100 welds, and any flaw in the process could lead to significant time, energy, and environmental wastage. The precision demanded by their short-pulse laser welding process required meticulous monitoring, pulse by pulse, to ensure stability. The use of a 300-watt, 1064 nm pulsed laser with specific RS-232 connectivity needs and a unique cable length added to the complexity.
Gentec-EO recognized the gravity of the issue and stepped in with a two-part solution to address the customer's pressing problem. Discover how their solution helped enhance and ensure precision, minimized defects, and helped the battery manufacturer improve their return on investment while aligning with their sustainability goals.
Get unlimited access to:
Enter your credentials below to log in. Not yet a member of Photonics Online? Subscribe today.