Case Study: An Enabling Technology For Optimized Automated Manufacturing
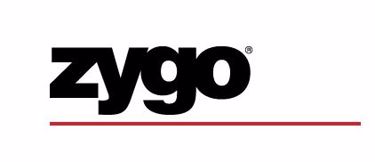
Challenge:
The exacting nature of the mirrors manufactured by Cambridge Technology require laser interferometry to measure the surface form of almost every precision beryllium mirror it produces. The company also depends on laser interferometry at various stages in the production lifecycle for a clear understanding of performance characteristics.
The company’s original laser interferometry solution was deficient in two key areas. First, it was prone to environmental vibrations, and second, measurement data was stored as individual text files (or text reports) which meant that it was extremely difficult to analyze.
Each unique mirror in the Cambridge Technology range required a different application which, in turn, required specific configuration of the laser interferometer.
To overcome these deficiencies, the company required a metrology solution that would promote process automation. They also needed a solution that would relieve manual workload while minimizing sensitivity to environmental vibration.
Get unlimited access to:
Enter your credentials below to log in. Not yet a member of Photonics Online? Subscribe today.