Advantages And Disadvantages Of Laser Welding
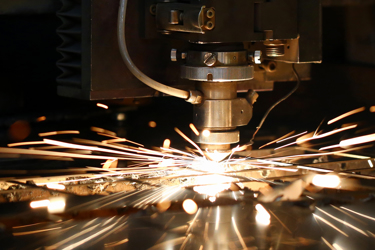
Laser precision allows for better quality welds, faster throughput, reduced post-processing costs and access to new domains of application.
The main drawback of laser welding is the hefty price tag for the equipment. Our accurate measurement solutions help you maximize the return of this investment.
ADVANTAGES OF LASER WELDING
MINIMAL THERMAL IMPACT ON THE SURROUNDING SURFACES
Welding, both traditional and laser-based, implies heat delivery at the junction between two surfaces. The melted metals mix and, after they’ve cooled, form a strong bond, effectively joining the two components together.
The problem with the traditional methods is that they do not deliver this heat only at the weld seam, but also in the surrounding material. The result is bending, stress, and other negative impacts on the material near the welds.
Lasers on the other hand, have enormous power density. In other words, they can deliver their heat extremely locally at the seam, leaving the surrounding materials in better condition.
Get unlimited access to:
Enter your credentials below to log in. Not yet a member of Photonics Online? Subscribe today.