Understanding Laser Safety In Fabrication Settings
By Ken Barat, CLSO, Laser Safety Solutions
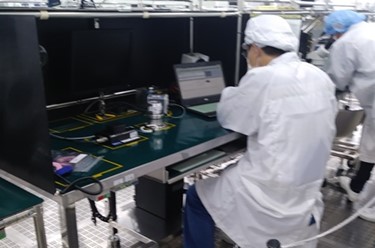
Many laser standards exist to address the variety of laser use applications. However, a review of such standards reveals the omission of at least one major laser use setting: the fabrication setting. This setting comprises a number of situations and activities, including rows of staff putting together a traditional laser, setting high power diode arrays together, and aligning such arrays into fibers.
These activities typically are performed in a repetitive fashion, so they are not eyed with the same scrutiny as research. Further, while staff performing this activity likely are highly skilled relevant to their specific tasks, they usually have little to no background in optics, laser physics, or biological effects.
Industrial laser standards, such as ANSI Z136.9 Safe Use of Lasers in the Manufacturing Environments and ANSI B11.21 Safety Requirements for Machine Tools Using a Laser for Processing Materials, do not apply to these staff or operations. The guidance found in Z136.1-2014 Safe Use of Lasers, ANSI Z136, and IEC 60825-14 are relatable, but do not match one-for-one.
So, what are the basic laser safety requirements for fabrication? In a nutshell: appoint a laser safety officer (LSO), train staff commensurate with a Class 3B and Class 4 laser user, establish a hazard zone, post warning signs, evaluate hazards, and put controls in place to mitigate those hazards. This article details what each of those actions might entail.
Getting Started
To begin addressing laser safety in a fabrication setting, organizations must first answer two broad questions of equal importance:
- What laser safety controls are relevant and meaningful to this work set-up?
- What level of laser safety training should staff performing and working around this operation receive (i.e., what laser safety awareness is relevant to them)?
A common work setting, I have observed is one or more rows of workbenches, sometimes with workbenches facing each other front and lined up side-to-side. Often, staff are attired in some level of clean room clothing; sometimes one person is wearing laser protective eyewear, while the person at the next station chooses not to wear eyewear. Other settings see people using a microscope and firing a laser to weld wires, jewelry, etc., in the same row. Often, the laser beam is fired within an enclosure.
Of course, with all of these varied setups, people are walking in the spaces between the rows, which prompts several questions: Are these passers-by at risk? More critically, what is the potential for exposure to those working with and around these systems?
To cite a more specific example, if a diode array is fixed in a holder, and one is trying to align fibers when there is an open beam path of less than 1 cm (or even a few millimeters) what are the chances of a hazardous reflection? If I have an open beam path, going into a power meter or some other analysis apparatus, consideration of the meter being out of place plays a real role in the safety evaluation, too.
It bears mentioning that sometimes, fabrication activities are short-term. In these cases, allocating space and resources for safety measures can be even more challenging. Regardless of the activity’s permanence, the following considerations should be weighed seriously.
User Training
All laser standards and regulations state that users of Class 3B and Class 4 Lasers or laser systems require laser safety training because of the biological hazard potential these laser classes present. Often overlooked, though, is that training only needs to address the level of potential hazard. Per: Z136.1-2014: “The level of training shall be commensurate with the degree of potential laser hazards, both from laser radiation and non-beam hazards.”
What this means to us is that training does not have to be comprehensive. It can cover the biological effects of the wavelengths involved without reviewing the physics of the laser. Laser control measure training need only address information required for the job at hand. Observation of the work setup and feedback from employees will inform the LSO which concerns must be addressed in training, and to what extent. Employee and management responsibilities for overall safety remain intact.
Overall, I strongly recommend some laser safety training in employee orientation. Make sure to state that lasers are in use, but controls are in place to keep staff safe, especially if “Danger - Laser” signs are conspicuously posted in the workplace; they do not work as motivational posters
Lets now turn to laser safety program elements.
Appoint a LSO — A laser safety officer must be appointed for any Class 3B or Class 4 work. Usually, this is a part time role, but it does require an understanding and appreciation of the laser hazards and controls.
Substitution of alternate controls — The LSO can evaluate all control measures (engineering and administrative) to determine whether they are appropriate; this is an essential duty of the LSO in fabrication settings, and it can save unnecessary efforts and money. If the LSO is uncomfortable with this tack, a consultant can be hired to provide outside evaluation of controls. Regardless, documentation of the reasoning and evaluation is required.
Auditing — The LSO must periodically visit laser use areas to determine the functionality of controls. In fabrication, I recommend this activity more than once a year, maybe once a quarter.
Classification — Standards state the LSO can accept the classification designated by the manufacturer. However, what happens when you are the manufacturer, implementing your fabrication setup at a stage before classification measurements can be taken? I recommend that controls should be guided by the system output during its intended activity. Note, too, that equipment used to make a laser is not a laser product unless it uses a laser itself.
Signage — Signage wording has been evolved and often includes two or more languages; the real challenge in fabrication settings is where to place signage. Formally, warning signs are required at boundaries between safe and non-safe zones: the nominal hazard zone (NHZ). The NHZ also marks the place where a decision must be made whether to don protective eyewear.
If there is a hazard communication sign at the workspace’s main entryway, a laser symbol also is warranted. Some place the laser warning signs at both ends of workbench rows. I also have seen warning signs posted at each work bench, which relays risk information to any individual walking past the work station. Regardless, if the work rows are in an area segregated by a laser curtain, signs need to go at each entrance to the area.
Area Warning Device (i.e., a “Laser On” indicator) — Area warning devices are a requirement for Class 4 work, and are recommended (though not technically necessary) for Class 3B work. I have seen a “Laser On” light at a work space’s curtain boundary (though that light rarely is connected to all lasers in the space), though such a light may be on at all times during a work shift. There also exist setups with “Laser On” lights at each work station, and many times these lights are used as a manual option.
Note that the area warning device does not have to be a light; a sign also can work. Per Z136.1-2014: “…a Class 4 laser-controlled area shall have an area warning device that is visible prior to entering the area. The purpose of the area warning device is to ensure that persons who are about to enter the laser-controlled area are aware that the laser is emitting or is about to begin emitting accessible laser radiation within the area.”
If the actual exposure hazard and nominal ocular hazard distance (when a reflection from the beam is no longer a hazard) is such that it does not extend beyond the workbench, the warning light is rather useless as a safety warning device. The same may be said for individual, bench-mounted warning signs, as these operations rarely have unattended live laser beams.
Standard Operating Procedures (SOP) — SOPs in the fabrication world really are the “work procedure.” The LSO should ensure the work procedure includes not just operational instruction, establishes safety that items are in place and being used (both laser and non-beam). A clever LSO might develop a SOP for the entire work area, listing hazards and how they are mitigated.
Emergency Stop (E-Stop) — Many user standards call for an E-Stop, but my experience in the Fabrication setting is that the common “mushroom” E-Stop is an unnecessary expense. The LSO can evaluate whether an E-Stop is needed, or an appropriately marked device to cut power or block the beam is acceptable (per the laser standards) — one should be more concerned about controlling electrical safety than shutting down a 3-cm beam path. I cannot think of a case in a fabrication operation when an evacuation would be required, versus shutting off the power at the power supply or pulling out a wire.
Windows — Any laser protective window must be labeled with its wavelength coverage and optical density. Sadly, this is not common, or the labeling is so small it is unreadable or goes unnoticed. While this labeling responsibility would seem to fall on the equipment manufacturer, if such windows or panels are not labeled, it falls to the facility to add appropriate labeling.
Hazard Evaluation
It is common for fabrication setup to be fixed in position, providing limited degrees of freedom, and meaning that the likelihood of stray beams is extremely limited if no foreign object is placed in the beam path. Hazard evaluation should take credit for this restriction, as barriers can effectively limit hazardous reflections. It is essential that the LSO perform a hazard evaluation, and repeat the tack as wavelength and power output evolve.
Laser Protective Eyewear — This safety item (discussed in a previous column) has deliberately been left for last. With proper controls, eyewear should not be required. Remember, if staff are wearing some level of clean room clothing, eyewear can add to their level of comfortability, reduce stress, and — most importantly — improve visibility. Remote viewing with a web cam or CCD camera also may offer several advantages to the work flow.
Summary
Laser use in the fabrication setting is an oft-overlooked challenge. Many traditional laser safety controls are not an easy fit — square pegs in round holes, so to speak — but that does not mean our square pegs cannot be shaved down enough to fit. An understanding of potential laser hazards is critical, as is a knowledge of how to implement time-honored control measures. No matter what, laser safety is our goal, and it is achievable.
About The Author
Ken Barat, CLSO, is the principal consultant at Laser Safety Solutions. He is the former Laser Safety Officer for Lawrence Berkeley National Laboratory and the National Ignition Facility. He is the author of several text books on laser safety. He has served as the laser safety adviser for Laser Interferometer Gravity Wave Observatory, ELI, and Allen Institute, among others. Laser Institute of America Fellow, Rockwell award winner and senior member IEEE & SPIE. Part of “Ask the expert” team for the Health Physics Society. The organizer and executive director of the first seven LSO Workshops.