Understanding Digital Twins In Metrology

By John Oncea, Editor
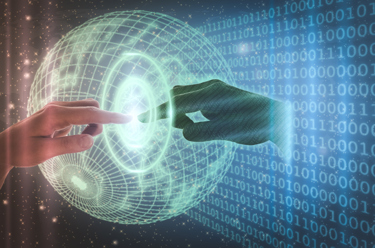
Digital twins enable real-time metrology precision by providing continuous monitoring and analysis of manufacturing processes, allowing for instant detection of defects and deviations from specifications.
There are digital twins, then there are DIGITAL TWINS!
Rolls-Royce is using digital twins as part of their “IntelligentEngine” program, Shell uses them to optimize production and increase the safety of their offshore platforms, and Pfizer is advancing their research and development efforts in the field of cancer thanks to them.
Then there’s Nvidia, a technology company that designs and sells graphics processing units (GPUs), application programming interfaces (APIs), and system on a chip units (SoCs). Oh, it also created a digital twin of the Earth.
Nvidia’s digital twin platform is called Earth-2 and it can simulate and visualize the Earth’s climate and weather patterns at an unprecedented scale and resolution. Earth-2 is a cloud-based platform that leverages advanced AI models to produce high-resolution climate simulations and forecasts up to 1,000 times faster than traditional computing methods and can visualize weather patterns with 2km detail globally.
The platform provides APIs enabling government agencies, weather forecasters, and climate tech companies to create AI-powered simulations of atmospheric conditions, cloud cover, extreme weather events like hurricanes and typhoons, and deliver real-time forecasts and warnings in seconds.
Early adopters include The Weather Company, which plans to combine Earth-2 with Nvidia’s Omniverse to create digital twins showing the real impact of weather, and Taiwan’s Central Weather Administration, which aims to improve typhoon forecasting and evacuation planning using advanced AI models.
As you can see, digital twins are capable of big things. Let’s take a look at this technology, as well as how the photonics industry is using it.
What Are Digital Twins?
Digital twins are virtual replicas of physical assets, processes, or systems. These digital counterparts mirror real-world entities in every detail, enabling comprehensive understanding and analysis. While the concept isn’t entirely new, recent advancements in sensor technologies, data analytics, and computing power have elevated the capabilities of digital twins to new levels.
“At its core, a digital twin is not merely a simulation but a dynamic digital replica intricately entwined with real-world phenomena,” Energy Central writes. “Initially conceived in manufacturing and engineering sectors, digital twins have transcended boundaries, finding applications in diverse domains, including architecture and city planning. Their evolution underscores a paradigm shift, from passive models to active agents driving insights and optimizations in complex systems.”
The integration of AI technology brings a new dimension to digital twins, enhancing their capabilities significantly. By leveraging the power of Big Data and machine learning algorithms, AI-equipped digital twin technology can navigate and decode the complex networks of urban environments. This empowers them to do more than just provide a static representation of the physical world. With AI, digital twins can become dynamic decision-making platforms that optimize energy consumption, predict traffic patterns, and much more.
The same benefits digital twins bring to urban management can be applied to photonics. According to IDW, digital twins, AI, and machine learning “are expanding the technological repertoire, which in the medium term will enable self-learning machines and first-time-right production. Cyberphotonics could thus provide the key to the ‘Internet of Sustainable Production,’ a field that Fraunhofer ILT in Aachen is building with various other institutes, and one in which a growing database is creating the basis to drive forward innovative process chains for the circular economy.”
6 Ways Metrology Is Changing The Game
As technology evolves, digital twins are emerging as a game changer in the field of metrology. One of the primary roles of digital twins in metrology is the precise identification of defects in manufacturing processes. Traditional quality control methods often rely on periodic inspections, sampling, and post-production analysis, which may not catch defects in real time or at an early stage. Digital twins are resolving this problem in the following ways:
- Real-Time Monitoring: Digital twins integrate with sensors and IoT devices deployed in the manufacturing environment to capture real-time data on dimensions, tolerances, and other relevant metrics. This data is processed by the digital twin, which compares it to the expected values and identifies any discrepancies indicating a defect. The digital twin processes this real-time data, comparing it to expected values and identifying any deviations that may indicate a defect. For instance, in a production line for precision components, a digital twin can monitor the dimensions of each part as it is being manufactured. If there’s any deviation from specified tolerances, the digital twin immediately flags the anomaly, allowing corrective action to be taken before defective products accumulate.
- Performing Real-Time Quality Control: Digital twins go beyond defect identification; they actively contribute to real-time quality control. By providing insights, feedback, and adaptive adjustments during the manufacturing process, they ensure that products meet stringent quality standards.
- Iterative Process Optimization: The continuous data flow from sensors to the digital twin allows for iterative optimization of manufacturing processes. As the digital twin identifies areas for improvement or deviations from quality standards, it suggests real-time adjustments to parameters such as machine settings, material composition, or process speed. For example, in a 3D printing environment, a digital twin can monitor the layer-by-layer deposition of material. If inconsistencies are detected, it dynamically adjusts the printing parameters, ensuring that each layer adheres to specified quality criteria.
- Adaptive Control Systems: Digital twins enable the implementation of adaptive control systems that respond dynamically to changing conditions. By analyzing real-time data, digital twins can adjust control parameters on the fly to maintain consistent product quality, even when raw materials, environmental factors, or machine performance varies.
- Predictive Analytics: Digital twins leverage predictive analytics to anticipate potential defects before they occur. By analyzing historical data and identifying patterns, the digital twin can predict when a machine or process is likely to deviate from desired quality standards, enabling preventive measures to be taken.
- Automated Exposure Time Selection: In structured light metrology systems, digital twins can automate the selection of optimal exposure time for repeated scanning, reducing the need for manual intervention and improving reconstruction accuracy.
By providing real-time monitoring, adaptive control, process optimization, and predictive analytics, digital twins enable manufacturers to produce high-quality products with unprecedented precision and efficiency in metrology and quality control processes.