Thin Film Coating: More Than Meets The Eye

By John Oncea, Editor
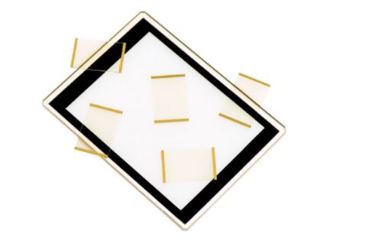
Thin film optical coatings are, according to our good friends at Abrisa Technologies, applied to optical substrates such as glass to alter or change their optical properties. The coating is applied in extremely thin layers to the surface and the number of coatings and the thickness of the coating is done to affect a specific wavelength of the light. Thin Film Optical Coatings from Abrisa Technologies are applied via electron beam and ion-assisted electron beam deposition influencing and controlling reflectance, transmittance, absorbance, and resistance.
The thin film multi-layer coatings can be applied to glass substrates as thin as 70 microns and as small as 0.1” and as thick as 6” and in diameters up to 36” and there are more than a dozen thin film optical coatings including:
- Indium Tin Oxide (ITO)
- Index-Matched Indium Tin Oxide
- Front & Back Surface Mirrors
- Dichroic Filters
- Band-pass Color Filters
- AR – anti-reflective Coatings
- Beam Splitters
- Metal Coatings
- Precision Hot Mirrors
- Cold Mirrors
- Neutral Density Filters
- Infrared or IR Filters
- Ultraviolet UV Filters
Several deposition methods are available for those seeking to apply thin films, notes A&A Coatings. Desired thickness, the substrate’s surface makeup, and the deposition purpose can determine the ideal method, of which there are two basic types: physical and chemical.
To produce thin films using the physical deposition method, thermodynamic or mechanical methods are relied upon. Generally, for functional and accurate results, these require low-pressure environments. Using the chemical deposition method, the substrate receives a deposited coating on its surface after being fully submerged in chemical fluid. This is done in a conformal pattern – meaning that an equal coating is applied to every one of the substrate’s surface.
With that understanding, let’s take a look at two thin film stories: magic solvents and technology enablers.
Magic Solvent Creates Strong Thin Films
A novel polymerization technique that utilizes reactive vapors has emerged, which can produce thin films with superior properties such as mechanical strength, kinetics, and morphology, notes the Cornell Chronicle. This method of synthesis is more eco-friendly compared to conventional high-temperature or solution-based manufacturing, and it holds the potential to enhance polymer coatings for microelectronics, advanced batteries, and therapeutics.
“This scalable technique of initiated chemical vapor deposition polymerization allows us to make new materials, without redesigning or revamping the whole chemistry. We just simply add an ‘active’ solvent,” said Rong Yang, assistant professor in the Smith School of Chemical and Biomolecular Engineering at Cornell Engineering. “It’s a little bit like a Lego. You team up with a new connecting piece. There’s a ton you can build now that you couldn’t do before.”
In semiconductor manufacturing and computer microchip production, Chemical Vapor Deposition (CVD) is a widely used technique to manufacture flawless inorganic nanolayer materials. However, due to the high-temperature requirement of the process, organic polymers do not perform well. To counter this limitation, low-temperature CVD polymerization techniques like initiated CVD (iCVD) have been developed for polymer synthesis. Nonetheless, according to Yang, this method has its limitations as people have reached the limit of the chemistry that can be achieved through this approach.
Yang’s and her team studied how vapor-deposited polymers interact with bacterial pathogens and how bacteria, in turn, colonize polymeric coatings, from the paint used in ship hulls to the coating for biomedical devices.
They developed a different approach to diversify CVD polymers by borrowing a concept from conventional solutions synthesis: the use of a ‘magic’ solvent, i.e., an inert vapor molecule, that isn’t incorporated into the final material, but instead interacts with a precursor in a way that produces new material properties at room temperature. ‘It’s an old chemistry but with new features,’ Yang said.”
After the researchers created a thin film, they brought it to Baker's lab for analysis. Through nanoindentation testing, they discovered that the solvation mechanism had strengthened the material. Additionally, the solvent caused the polymer coating to grow faster and change its shape.
This newly discovered technique can be applied to various methacrylate and vinyl monomers. It can be used for anything with a polymer coating, including dielectric materials in microelectronics, anti-fouling coatings in ship hulls, and separation membranes that enable wastewater treatment purification. Moreover, this method may allow researchers to adjust the permeability of pharmaceutical products for controlled drug release.
Thin Film Coating As An Enabling Technology
“As long as there are optical systems, optical coatings will be necessary,” writes Novus Light. “And it is thin-film technology which allows these optical systems to fulfill their incredible potential.”
Novus Light adds, “The growth of computer technology made high-density systems of storage obligatory, and it is this which has driven frantic research and development, specifically on optoelectronics, magnetic and optical properties of thin films.”
Manufacturers who can enhance substrate materials using various deposition materials can cater to the unique requirements of numerous specialized applications. As device miniaturization gains more popularity, it also leads to reduced costs related to equipment and processes. Industries such as engineering, magnets, and energy, and applications like neurological sensors, optical memories, and friction reduction, still require innovative solutions from our field.