The Cobots Are Coming! The Cobots Are Coming!

By John Oncea, Editor
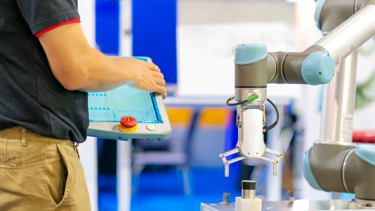
Using 2D or 3D vision to guide robots can improve flexibility and lower costs in various industrial applications. With the rise of collaborative robots, also known as cobots, there are now more opportunities to integrate machine vision into the work environment.
Collaborative robots, or cobots, were invented in 1996 by a pair of Northwestern University engineers and are designed to work alongside humans in shared workspaces, offering unique solutions for real-world problems.
The International Federation of Robotics, a global industry association of robot manufacturers and national robot associations, recognizes two main groups of robots: industrial robots used for automation in industrial settings, and service robots designed for both domestic and professional use. In the context of photonics, cobots can play various roles in assisting with tasks related to photonics research, manufacturing, and other applications.
Service robots are often referred to as cobots because they are intended to work in collaboration with humans. In the past, industrial robots were kept separate from humans by fences or other protective barriers, but cobots eliminate this distance.
Machine vision can be integrated with cobots to provide an additional tool to improve production processes, gain efficiencies, reduce floor space requirements, and stay competitive. According to WiredWorkers, “Vision systems consist of 2D or 3D cameras that give the cobot vision. These allow cobots to locate objects, recognize patterns or scan QR and barcodes.
“Vision can make integrating a cobot a lot easier. In a normal situation, objects must be presented to a robot in a structured way so that the robot knows where to go to pick up the objects. With vision, the cobot can locate objects and structured feeding is no longer necessary. It is also possible to use a vision system to carry out optical inspections, for example checking objects for abnormalities.”
Many modern cobots are equipped with advanced technologies such as artificial intelligence (AI) and the Internet of Things (IoT). These technologies enable cobots to learn and adapt to their environment, enhance their capabilities, and communicate with other machines or systems.
What Are These Cobots You Speak Of?
The IFR categorizes cobots in four ways: coexistence, sequential collaboration, cooperation, and responsive collaboration. Coexistence is defined as humans and robots working alongside each other without a fence but with no shared workspace. Sequential collaboration requires humans and robots to work in a shared workspace, but their motions are sequential (they do not work on a part at the same time).
Cooperation is when robots and humans work on the same part at the same time, with both in motion and responsive collaboration occurs when the robot responds in real-time to the movement of the human worker. Most of the industrial applications of cobots today are coexistence or sequential collaboration.
Cobots are equipped with force sensors, torque limiters, vision systems, and proximity sensors. If a cobot comes into contact with a human or detects an obstruction, it can quickly stop or slow down its movement to prevent injury.
A cobot's user-friendly interface allows operators to program and control them easily, even without advanced programming skills. Some cobots can be programmed through intuitive graphical interfaces or by physically guiding the robot's movements, a process known as teaching.
Designed to be easily reprogrammed and reconfigured for different tasks, cobots are highly versatile and suitable for environments where tasks might change frequently. While cobots can be an initial investment, they are often considered more cost-effective than traditional robots due to their easy setup, reduced need for specialized programming, and the ability to repurpose them for different tasks.
Cobots And Photonics: Two Great Technologies That Go Great Together
The integration of cobots and photonics processes requires careful planning, programming, and consideration of safety protocols. Proper training for operators and programmers is essential to ensure the cobots are used effectively and safely. As technology advances, the capabilities of cobots in photonics applications will likely continue to expand, enabling more sophisticated and efficient processes in the field. Following are several instances of how cobots can benefit the field of photonics:
- Precision Assembly and Manufacturing: Photonics often involves the fabrication and assembly of delicate and precise components such as optical fibers, lenses, and mirrors. Cobots can be programmed to perform tasks like picking and placing these components with high precision, minimizing the risk of human error and contamination. Their ability to work with consistent accuracy is crucial in maintaining the quality of optical systems.
- Optical Alignment and Testing: Cobots can be used to automate the alignment and testing of optical systems. They can manipulate and adjust optical elements to achieve optimal alignment, ensuring that light is properly focused and transmitted through the system. Cobots equipped with cameras and sensors also can assist in verifying the performance of optical components and systems.
- Laser Processing: Lasers are extensively used in photonics applications for cutting, engraving, welding, and marking. Cobots can be integrated with laser systems to perform these tasks with high precision and repeatability. They also can enable more complex laser processing tasks by providing better control over the laser beam's position and intensity.
- Quality Control and Inspection: Cobots can be programmed to inspect optical components and systems for defects, scratches, or imperfections that might affect their performance. They can use cameras, sensors, and imaging techniques to identify deviations from specifications and notify human operators when intervention is needed.
- Laboratory Automation: In research and development laboratories, cobots can assist researchers by performing repetitive tasks such as sample handling, data collection, and experimental setups. This helps scientists focus on higher-level tasks that require creativity and critical thinking.
- Material Handling and Packaging: Cobots can be employed to handle and package delicate optical components, ensuring that they are transported and stored without damage. This is particularly important in the production and distribution of photonics products.
- Training and Assistance: Cobots can be used to train new operators in photonics manufacturing processes. They can guide operators through steps, providing visual cues and feedback to ensure that procedures are followed correctly.
- Safety Enhancement: Cobots are designed to work safely alongside humans. In photonics environments, where precision tools and delicate components are present, cobots can help reduce the risk of human injury by taking over tasks that involve potential hazards.
The integration of photonic technologies and cobots can impact numerous industries, including manufacturing. Here, cobots equipped with photonics-based sensors such as vision systems using lasers or cameras can inspect products for defects or irregularities. Laser-guided cobots also can assist in precise assembly and welding processes.
In medical settings, cobots can work with photonics-based tools, such as laser scalpels, for minimally invasive surgeries. Photonics-based sensors also can enhance the accuracy of robotic-assisted procedures.
Cobots combined with photonics-based navigation systems can optimize warehouse management, improving logistics by autonomously moving goods while avoiding obstacles. In agriculture, photonics-enabled sensors can be used to monitor crop health and growth, while cobots equipped with these sensors can perform targeted actions like selective harvesting.
Finally, in research and development, photonics can enhance the capabilities of cobots in research environments, enabling them to carry out tasks like precise measurement, data collection, and analysis.