Smart Lasers + AI = Revolution

By John Oncea, Editor
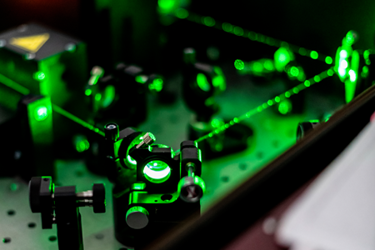
Smart lasers with artificial intelligence capabilities are emerging as a revolutionary technology in manufacturing and industrial applications.
TRUMPF recently announced it had entered into a strategic partnership with SiMa.ai to develop artificial intelligence (AI) chips and software to improve welding, cutting, and marking processes. The collaboration intends to accelerate complex material processing in multiple industries, including electric vehicles (EVs).
Integrating SiMa.ai’s machine learning system on chip (MLSoC) technology with TRUMPF’s laser application expertise is expected to result in AI-optimized sensor technology that can monitor the quality of the laser welding process in real time and evaluate more than 3,000 images per second. In EV production, for example, the real time quality inspection during laser welding – aided by AI – is expected to replace separate and complex testing procedures. Moreover, battery manufacturers will be able to increase the quality of their production in real time and reduce the reject rate which could lower the price of electric cars for consumers.
At-Home, On-Demand Manufacturing
TRUMPF and SiMa.ai aren’t the only companies integrating lasers and AI – researchers at the University of Tokyo are, too.
According to Nature, the University of Tokyo’s Yohei Kobayashi and Hiroharu Tamaru, are using AI “to better understand the complex physics underlying the way lasers cut, weld or drill materials (to) make possible internet-based control of laser production systems, so that we can manufacture the things we want, on-demand, from home.”
“We have constructed an all-automated and autonomous data acquisition system, called the Meister Data Generator,” says Kobayashi, a professor at the University of Tokyo’s Institute for Solid State Physics. “We don’t even need to go to the lab to take data: it keeps working 24 hours a day, 7 days a week.”
Kobayashi and Tamaru have expanded their approach to encompass various laser production processes, with a recent focus on laser ablation. This technique involves using brief pulses of light to remove minute quantities of material from a surface.
To study this process, they developed a high-quality dataset by directing light pulses with adjustable durations at a solid target. The resulting surface changes were captured using a three-dimensional microscope, which produced images at a rate of approximately one per minute, allowing for the collection of around 1,000 data points in a single day.
The application of Big Data analysis to laser ablation processes is opening up new possibilities for precision manufacturing and material science research, and the University of Tokyo and Kyushu University in Fukuoka are already leveraging this approach to benefit the semiconductor manufacturing industry.
The ability to generate large, high-quality datasets rapidly and analyze them effectively is transforming the field of laser-material interactions. This approach not only enhances our understanding of the fundamental processes involved in laser ablation but also paves the way for optimizing industrial applications.
As researchers continue to refine these techniques, we can expect to see further advancements in laser-based manufacturing processes, particularly in industries that require high precision and control, such as semiconductor fabrication.
Lasers, AI, And Data Centers
AI networks rely heavily on the rapid processing and transfer of vast amounts of data to function effectively. This data-intensive nature necessitates robust infrastructure, with lasers playing a crucial role in enhancing efficiency and speed.
According to EFFEC Photonics, AI networks operate through two primary processes: training and inference. Training involves feeding large datasets into models to enable learning and prediction capabilities, while inference utilizes these trained models to make real-time decisions.
Lasers are instrumental in powering these processes by facilitating high-speed data transfer within data centers and across networks. They enable the rapid movement of information required for both the intensive computations of AI training and the low-latency responses needed for AI inference.
In data centers, lasers are essential for creating high-speed optical interconnects that reduce latency and improve energy efficiency, which is critical for real-time AI tasks. As AI technology continues to advance, the role of lasers in AI infrastructure is expected to grow, supporting the increasing demands for faster, more efficient data processing and transfer in AI applications.
Future Implications
The integration of AI with laser systems has far-reaching implications, fueling a manufacturing revolution. Personalized, on-demand manufacturing could become possible through internet-based control of AI-enhanced laser production systems. In addition, AI will help researchers better grasp the complex physics of laser-matter interactions. And beyond data centers, AI-enhanced lasers are transforming edge computing, 5G/6G networks, and other advanced applications.
As this technology continues to evolve, we can expect to see even more innovative applications and improvements in manufacturing efficiency, quality control, and data processing capabilities across various industries.