Recognizing Ergonomic Concerns In The Laser Lab
By Ken Barat, CLSO, Laser Safety Solutions
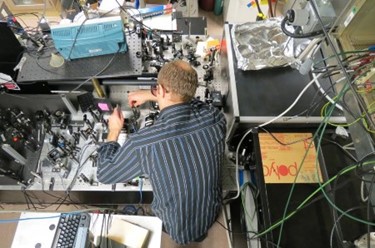
It is common practice for those working behind a desk to receive an ergonomic evaluation.
They may wind up with clever upright workstation; Items such as document holders, an ergonomic chair, and a different style computer mouse may be purchased. Attention is given to workspace location and the computer monitor’s height/eye level is assessed. Keyboard style and placement -- trying to avoid hard and sharp surfaces for wrists to lean on – also are among the concerns recognized and reviewed. Finally, staff may be instructed on proper posture and/or hand positioning.
However, this concern for comfort and safety does not seem to be consistently granted to those assigned to a laser lab. The most common explanation I hear for this oversight is that lab staff spend limited time at workstations in laser labs ― something many a graduate student might disagree with. Reach-in issues ― a major concern in laser set-ups, which effects back torque ― go completely unaddressed. Makeshift workstations are set up either on desks or using optical tables, placed wherever they seem to fit.
To improve the safety, positive working environment, and ― ideally ― effectiveness of your laser lab, weigh the following ergonomic considerations when approaching its layout:
Reach-in problems and accessibility ― Reach-in problems and accessibility often are overlooked until lab set-up completed. Not only can this present difficulty for one’s work during alignment, it can lead to back injuries. Related to reach-in difficulties is the need to use platforms to enable technicians or researchers to reach components higher or deeper in the set-up. Related, lab staff then must find or create space for such platforms.
Makeshift workstations ― Key boards often are placed in positions that can contribute to carpal tunnel or other injuries: on the edge of sharp optical table edges, on top of equipment, blocking cooling holes (something I have observed many times), etc. One solution is the use of swing arms that can be attached to the table or hang from shelving above the optical table.
Prolonged standing ― As documented in many industries and work environments, prolonged standing by staff can increase fatigue and lead to posture problems. Antifatigue mats are a simple solution, but they are rarely found in laser labs.
Enclosure and removeable panels around optical set-ups ― While such items are advantageous for containing stray reflections and diffuse light, they present their own ergonomic challenges. Note the positioning of handles used to remove/lift these panels ― is it acceptable for safe handling/lifting (removal) of the panels, given their weight? One also needs to consider lab staff and their capabilities for lifting. A hydraulic system is one solution, but that is not always an easy or economical fix.
Positioning of monitors ― Monitor viewing perspective in the laser lab is rarely take into account. This can lead to neck strain, as well as make it challenging to actually see the displayed information. As always, when it comes to seeing colors and information on the monitor, laser eyewear effects come into play. How the information is displayed is a science in itself.
Control room set-up ― One might think that the need, and design for, a control room in high-dollar laser facilities ― such as petawatt lasers ― would be scrutinized in-depth; funds would be allocated to design such an important area. However, experience has shown that is not always the case. Indeed, in some control rooms I have seen, operators cannot see all relevant displays when sitting at their work station.
Trip hazards ― Cables and hoses are common components in laser labs. Typical solutions are “go high” (overhead) or “go low” (path along the floor). The floor is the most natural location, and trip hazards most often are addressed by “bridges” made of wood (whose combustibility must be considered) or metal (wherein grounding might be needed, depending what is under the bridge). The best floor solution is heavy duty plastic bridges, with pre-formed groves for cables and hoses, which can be securely linked together. The “high” approach most often takes the form of cable trays, hanging from the ceiling. Electrical cable connections can be dropped from the ceiling.
Another approach is to run cables and hoses through cable trays, but beware: there are rules on what can be laid in a cable tray and how it can be placed there. Cable trays come in different varieties; in the United States, the National Electric Code (NEC) and National Electrical Manufacturers Association (NEMA) — the latter an association comprising major cable tray manufacturers in the industry —have codes and recommendations of what can be laid out in such trays, as well as separation techniques. For the NEC, it is articles 250, 318, and 800.
An example would be restrictions on having water lines and power cords in the same tray without some separation barrier. These restrictions also address problems from possible electromagnetic interference (EMI).
Lighting ― Some operations allow for a well-lit room; other experimental set-ups need low lighting due to photon contamination concerns. In either case, task lighting may be needed, as well as fluorescent strips on the floor to clearly indicate the direction of exits in case of an emergency.
Lifting — While not thought of as typical laboratory activities, lifting and other physical activities are common; turbo pumps, dye pumps, scroll pumps, and related vacuum pumps and equipment need to be positioned and moved in labs. Some of these devices exceed the 40 lb/ 18.1 kilo limit that many ergonomists consider the maximum weight for a single individual to lift without assistance.
Noise/Vibrations — Related to pumps above is noise. Pumps and standalone air-handling units can easily produce excessive nose and vibrations, which may require these devices to be placed outside of the use area.
Conclusion
The American National Standards Institute (ANSI) standards on laser safety ― endorsed by the Laser Institute of America ― as well as similar international IEC user standards, all recognize that non-beam hazards need to be addressed in the laser use environment. Ergonomic hazards should be part of any non-beam hazard evaluation.
One way to help address ergonomic concerns is to add ergonomic evaluation to the list of topics covered by LSO audits of a laser control area. Until people start planning for and reviewing these factors, little will change.
About The Author
Ken Barat, CLSO, is the principal consultant at Laser Safety Solutions. He is the former Laser Safety Officer for Lawrence Berkeley National Laboratory and the National Ignition Facility. He is the author of several text books on laser safety. He has served as the laser safety adviser for Laser Interferometer Gravity Wave Observatory, ELI, and Allen Institute, among others. Laser Institute of America Fellow, Rockwell award winner and senior member IEEE & SPIE. Part of “Ask the expert” team for the Health Physics Society. The organizer and executive director of the first seven LSO Workshops.