Optical Hardware And Intelligent Systems Powering Industry 4.0

By John Oncea, Editor
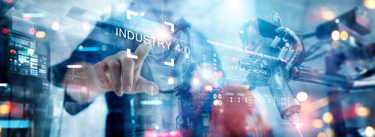
Optical hardware and intelligent systems are revolutionizing automated manufacturing, enabling real-time data, seamless integration, and smarter Industry 4.0 factories.
The fourth industrial revolution, Industry 4.0, is fundamentally altering the manufacturing landscape. Central to this transformation are optical hardware and intelligent systems, which form the backbone of automated, interconnected, and data-driven production environments. These technologies enable factories to operate with unprecedented speed, precision, and adaptability, creating smart manufacturing ecosystems that are agile, efficient, and resilient.
The Role Of Optical Hardware In Industry 4.0
Optical hardware, including advanced machine vision cameras, photonic sensors, and high-speed optical communication modules, is essential for modern automated manufacturing. These components enable machines to “see,” measure, and communicate with a level of detail and reliability that was previously unattainable.
Recent advances in optical hardware have been showcased at major industry events, highlighting the rapid evolution of photonic integration, high-bandwidth optical transceivers, and coherent transmission systems. For example, the 2025 OFC conference featured breakthroughs in photonic integrated circuits (PICs), which are now key to next-generation optical networking and enable the seamless interconnection of thousands of devices within smart factories. These advances, according to Connector Supplier, provide the high-speed data transfer and low latency required for real-time automation and AI-driven processes.
Fiber optics have become the preferred medium for connecting not only data centers but also production lines, supporting the massive bandwidth demands of AI-powered manufacturing. Semtech adds that the deployment of 1.6T optical transceiver modules, operating at 200G per lane, marks a significant leap in bandwidth capability, ensuring reliable communication and maintaining link quality even as the density and complexity of manufacturing systems increase.
Intelligent Systems: The Brains Of Smart Manufacturing
While optical hardware forms the eyes and nervous system of Industry 4.0, intelligent systems – powered by artificial intelligence (AI), machine learning, and advanced analytics – serve as the brain. These systems process the vast streams of visual and sensor data generated by optical devices, transforming raw information into actionable insights.
According to Ultralytics, AI-powered machine vision systems are now capable of performing complex inspection, measurement, and quality control tasks with a level of accuracy and speed that surpasses human operators. For instance, deep learning algorithms can detect subtle defects in products, optimize assembly processes, and even adapt to new manufacturing scenarios without extensive reprogramming. This continuous improvement loop is a hallmark of Industry 4.0, driving higher efficiency and product quality.
EasyODM adds that the integration of AI and machine vision is transforming manufacturing into a data-driven enterprise. Real-time data capture and analysis enable factories to make informed decisions, predict equipment failures before they occur, and continuously optimize production processes. This predictive capability minimizes downtime, reduces waste, and ensures that manufacturing systems can quickly adapt to changing market demands.
Seamless Integration: The Industrial Internet Of Things
The convergence of optical hardware and intelligent systems is made possible by the Industrial Internet of Things (IIoT). In modern factories, a dense network of sensors, cameras, and actuators – many of which rely on optical technologies – is interconnected via high-speed networks. This infrastructure enables real-time monitoring, control, and optimization of every aspect of production.
IIoT devices generate vast amounts of data, which are processed at the edge or in the cloud to provide immediate feedback and long-term insights, Robro Systems writes. Edge computing is particularly important for time-sensitive applications, as it allows data to be processed close to where it is generated, reducing latency and enabling faster decision-making.
Cloud-based machine vision and analytics solutions are also gaining traction, offering scalability and flexibility for manufacturers operating across multiple sites. These platforms facilitate the deployment of AI algorithms, enable remote monitoring, and support continuous improvement through centralized data analysis.
Real-World Impact: Automation, Efficiency, And Quality
The integration of optical hardware and intelligent systems delivers tangible benefits across the manufacturing sector. According to SG Analytics, automated workflows, powered by machine vision and AI, reduce the need for manual intervention, minimizing errors and increasing throughput. Robots equipped with advanced vision systems can perform intricate assembly, inspection, and sorting tasks with high precision, enabling manufacturers to achieve higher levels of productivity and consistency.
Proton Products adds that smart factories leverage real-time data to optimize resource allocation, reduce energy consumption, and enhance sustainability. Predictive maintenance, enabled by continuous monitoring of equipment health through optical sensors, minimizes unplanned downtime and extends the lifespan of critical assets. These capabilities are essential for maintaining competitiveness in a fast-evolving global market.
Data-Driven Decision Making And The Smart Data Path
A defining feature of Industry 4.0 is the ability to turn data into insight and action. Optical hardware captures high-fidelity data from every stage of the manufacturing process, while intelligent systems analyze this information to identify trends, anomalies, and opportunities for improvement. This data-driven approach, according to Telefónica Tech, supports informed decision-making, enhances operational efficiency, and drives continuous innovation.
The concept of the “Smart Data Path” encompasses the entire journey of data, from secure collection and transmission to advanced analytics and actionable outcomes. Cybersecurity is integral to this process, ensuring that sensitive production data remains protected even as it flows across interconnected networks.
The Future: Toward Fully Autonomous Manufacturing
As optical hardware and intelligent systems continue to advance, the vision of fully autonomous manufacturing comes closer to reality. According to Phys.org, next-generation photonic-electronic platforms are achieving unprecedented energy efficiency and bandwidth density, paving the way for AI hardware that can handle the demands of large-scale, real-time production environments.
Digital twins – virtual replicas of physical processes – are being used to simulate, monitor, and optimize manufacturing systems in real time, further enhancing agility and resilience. Augmented reality (AR) and virtual reality (VR) technologies, powered by high-resolution optical hardware, are transforming training, maintenance, and collaboration in complex industrial settings.
Optical hardware and intelligent systems are the linchpins of Industry 4.0, enabling the creation of automated, interconnected, and data-driven manufacturing environments. By providing the eyes, nerves, and brains of modern factories, these technologies are driving unprecedented levels of efficiency, quality, and adaptability. As photonic and AI innovations continue to accelerate, the future of smart manufacturing promises to be more connected, intelligent, and sustainable than ever before.