Master Machine Health With Advanced Sensors For Predictive Maintenance

By Emily Newton
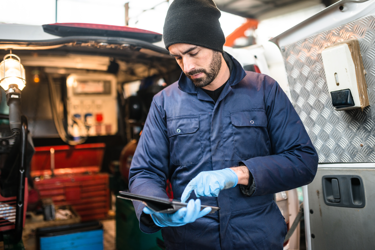
Maintenance is a dire but often underserved need. While most professionals understand that they should maintain equipment to avoid breakdowns and extend its life, fewer take the best approach in doing so. Implementing sensors for predictive maintenance is a necessary step forward.
Predictive maintenance is the practice of predicting repair issues by monitoring real-time equipment data. It’s a sophisticated approach requiring advanced technology but a highly beneficial one.
How Predictive Maintenance Sensors Benefit Businesses
Tracking machine health with sensors means businesses can recognize emerging problems before they’re noticeable to human eyes. Sensor data is also more precise than manual inspections, making predictive maintenance the most accurate upkeep method, which produces two primary benefits.
First, organizations can prevent a larger number of breakdowns because they can be confident they provide all the repair a machine needs. Secondly, they minimize downtime by preventing the repairs they don’t require. Sensors reduce human error and offer wirelessly accessible data, removing the need for routine inspections.
As predictive maintenance sensors enable higher uptime and efficient repair strategies, they result in lower ongoing costs. Equipment life spans also will lengthen as their operators ensure the machine remains in top condition for the longest possible time. Consequently, even if these sensors add technology costs up-front, they’re a cost-effective solution in the long run.
Types of Sensors for Predictive Maintenance
Warning signs of impending disrepair vary between systems. Likewise, the types of sensors for predictive maintenance vary depending on the application.
Temperature Sensors
Temperature sensors are among the most widely used, as excess heat is typically unideal. It also can be easier to detect before other signs are noticeable. For example, deteriorated insulation is the most common cause of transformer failure, and insulation fails in the presence of high temperatures. Consequently, detecting heat spikes enables earlier, more effective fixes.
In other cases, sensing technologies must monitor the high and low ends of a temperature range. Tracking both sides offers greater assurance that equipment remains in ideal operating conditions.
Vibration Sensors
Other predictive maintenance sensors gather vibration data. Excessive motion could signify moving parts needing realignment, tightening, or lubrication. In other contexts, it can suggest components that aren’t supposed to move are shifting.
Vibration sensors come in many forms. Some detect motion by sending a laser between two points and registering movement when one doesn’t align with the other. Alternatively, they may use a gyroscope or other method of detecting relative movement on a fixed point. Which solution is best depends on the specific application.
Current Sensors
Abnormal electrical signals may also indicate emerging maintenance issues. While some fluctuations in voltage, current, and resistance are to be expected, large enough discrepancies can be an early warning sign of a considerable problem, especially in high-power systems.
Electrical-related maintenance concerns are growing increasingly prominent, too. Roughly 70% of transmission lines in the U.S. are nearing the end of their serviceable life, making grid issues more common. Detecting early warning signs through current sensors helps businesses get ahead of such concerns.
Pressure Sensors
Pressure is another typical signal of something being wrong with a piece of equipment. Excessive air pressure in a pneumatic system or physical strain on a metal bearing can quickly turn into a massive, costly problem. Consequently, real-time warnings of these stresses offer a critical advantage.
Placing multiple pressure sensors throughout a machine provides even better insight. Differences in readings between sensing points help identify location-specific issues or narrow down what is causing the situation.
Implementing Predictive Maintenance Sensors
Choosing the right technology for the job at hand is the first step in applying sensors for predictive maintenance. Despite this practice’s potential, some companies have seen higher downtime and no savings after implementing it, highlighting how complicated it can be. The most important measure is to minimize false positives, and better sensor selection is the key.
Before buying any sensing technologies, organizations must determine the kinds of issues they’re likeliest to see or most need to prevent. They can then identify what metrics to track to predict such breakdowns. Once the key indicator is clear, businesses can recognize which type of sensor suits their needs.
Sensor fusion — combining input from multiple technologies — will provide the greatest accuracy and lowest false positive rate. However, implementing a wider range of sensing endpoints will incur higher up-front costs. Consequently, businesses should restrict this method to particularly sensitive or breakdown-prone equipment to ensure a positive return on investment.
Many predictive maintenance sensors use Internet of Things (IoT) connectivity to send data between endpoints. While efficient, IoT solutions introduce security concerns — there were over 112 million IoT attacks in 2022 alone. Facilities opting for these sensor technologies must also implement cybersecurity measures like data encryption, network segmentation, and automated breach detection. A third-party security provider may be necessary to achieve such protection.
Maintenance Can Gain Much From Advanced Sensors
While implementation is not always easy, using advanced sensors for predictive maintenance can yield huge benefits. Learning how this technology can improve a company’s bottom line is the first step toward a better upkeep program. As more organizations take advantage of this field, the industry as a whole will grow increasingly agile and cost-effective.