Laser Applications In Machine Vision

By John Oncea, Editor
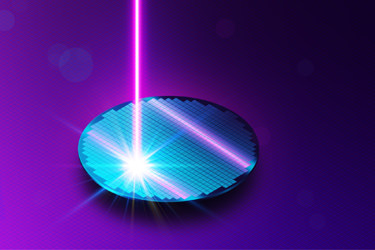
Laser technology plays a crucial role in machine vision, enhancing precision and enabling various applications.
Lasers are commonly used in machine vision as illumination sources because they can be focused to fine lines or dots that illuminate a small surface area. This allows imagers to measure roughness, pits, or scratches with high resolution.
Lasers are used in machine vision to enable 3D measurement systems for sorting, inspection, and defect detection. Laser diode modules are used to capture images, analyze, and automate tasks such as counting and inspection. Machine vision systems use software and advanced hardware components to perform these functions with greater precision, reliably, and at higher speeds.
Lasers can detect the spatial contours of unmoving and moving objects. This allows users to detect edge gaps, diameter, presence, and defects, to measure and subsequently correct or align them.
4 Laser-Based Applications
Lasers offer coherent, monochromatic light for high-contrast, low-noise imaging in machine vision. They support interferometric methods, 3D imaging, and surface topology analysis. These applications empower industries across manufacturing, robotics, and automation.
- Laser Triangulation: Laser triangulation is a common application where a laser line is projected onto an object. An imaging camera captures the lateral displacement and distortion of this laser line. By analyzing the recorded camera image, a 3D height profile of the object can be determined. It’s widely used for surface profiling, quality control, and precise measurements.
- Laser Diffraction Measurements: This technique utilizes telecentric laser beams (minimal divergence) to evaluate the diameter of an object by analyzing the Fresnel diffraction pattern of the shadow edge. Commonly employed for particle size analysis, especially in industrial and scientific settings.
- Measurement: In particle counting and measurement, a detector registers light reflected by particles passing through a laser beam. Used for quality control, identifying contaminants, and assessing particle size distribution.
- Width and Gap Measurement Utilizes the small emitter size of laser diodes (typically 1 µm x 3 µm) to measure widths and gaps. The shadow or diffraction pattern of an object placed in the laser beam provides information. Ideal for assessing gaps, tolerances, and dimensions.
Overcoming The Challenges Of Lasers
While lasers offer significant advantages in machine vision, there are also several challenges associated with their use. For instance, lasers can be hazardous to human eyes and skin. High-power lasers, especially in the visible and near-infrared spectrum, pose risks of retinal damage and burns. However, implementing safety measures such as laser safety goggles, interlocks, and proper enclosure designs, along with compliance with laser safety standards, can mitigate these concerns.
Laser light can scatter or reflect off surfaces, leading to unwanted interference which affects accuracy and reliability. The use of anti-reflective coatings, polarizers, and beam-shaping optics, as well as proper alignment and positioning, can minimize scattering effects.
Ambient light (sunlight, artificial lighting) also can interfere with laser-based measurements, affecting the signal-to-noise ratio but employing modulation techniques (e.g., frequency modulation) can distinguish laser light from ambient light. Shielding and filtering also can reduce interference. Other issues and fixes include:
- Surface Reflectivity Variation: Different materials exhibit varying reflectivity. Highly reflective or transparent surfaces can distort laser patterns.
- Mitigation: Calibrate systems for specific materials. Adaptive algorithms can compensate for reflectivity variations.
- Depth of Field and Working Distance: Laser triangulation systems have limited depth of field. Maintaining accurate measurements across varying distances can be challenging.
- Mitigation: Opt for telecentric lenses, adjust working distances, and consider multiple laser lines for extended depth of field.
- Temperature and Environmental Effects: Temperature fluctuations affect laser wavelength and refractive index, impacting measurement accuracy.
- Mitigation: Use temperature-stabilized laser sources and environmental enclosures. Compensation algorithms can correct for temperature-induced changes.
- Vibration and Mechanical Stability: Vibrations from machinery or external sources introduce noise into laser-based measurements.
- Mitigation: Stabilize optical components, isolate vibrations, and employ vibration-resistant mounts.
- Alignment and Calibration: Precise alignment of lasers, cameras, and optics is critical. Calibration drift over time can lead to inaccuracies.
- Mitigation: Regularly calibrate systems, use reference objects, and automate alignment procedures.
- Cost and Complexity: High-quality laser systems can be expensive. Integration and maintenance require expertise.
- Mitigation: Evaluate cost-benefit trade-offs. Consider off-the-shelf solutions and consult experts for system design.
- Power Efficiency and Heat Dissipation: High-power lasers generate heat, affecting stability and longevity.
- Mitigation: Efficient cooling mechanisms (e.g., Peltier coolers) and thermal management are essential.
Precision And Versatility For All
Lasers are indispensable tools in machine vision, offering unparalleled precision and versatility for a wide range of applications across industries such as manufacturing, robotics, and automation. From laser triangulation for 3D profiling to laser diffraction for particle size analysis, these technologies enable high-contrast, low-noise imaging, supporting interferometric methods, surface topology analysis, and more.
However, their use comes with challenges, including safety concerns, interference from ambient light, and issues related to surface reflectivity, depth of field, temperature fluctuations, vibrations, alignment, and cost. Nonetheless, by implementing appropriate safety measures, modulation techniques, calibration strategies, and technological advancements in cooling mechanisms and thermal management, these challenges can be effectively addressed. With continued innovation and expertise in system design and integration, laser-based machine vision systems will continue to play a vital role in enhancing productivity, quality control, and efficiency across various industrial applications.