Improving The Accuracy And Effectiveness Of Nanopositioning Systems

By John Oncea, Editor
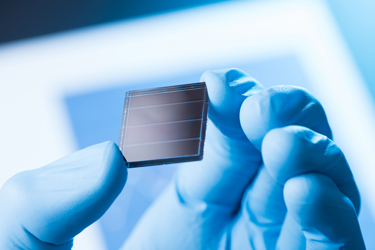
The effectiveness and accuracy of nanopositioning systems are being enhanced through advanced control methods, high-resolution sensors, and innovative mechanical designs. These improvements are essential for meeting the stringent requirements of modern nanotechnology applications.
Jacques and Pierre Currie showed, in 1880, that when a mechanical force is applied to quartz or other crystals, it generates an electric charge within the crystal. This became known as the piezoelectric effect. They also demonstrated that an electrical field causes the crystal to expand or contract, which subsequently became known as the inverse piezoelectric effect.
The Curries didn’t know that one day their discoveries would become a foundation of nanopositioning systems, a technology designed to produce repeatable, high-precision movements in increments of one nanometer or less over a distance of a few microns.
According to AZoNano, “A nanopositioning system is typically used to move and position devices such as sensors, probes, or scanners. Nanopositioning systems need to move the device to a set position and hold it precisely in place for extended periods or position, hold and reposition the device multiple times at high speeds.”
Nanopositioning systems are widely used in fields such as scanning probe microscopy, nanofabrication, data storage, and precision optics. The continuous improvement in control techniques, sensor technologies, and mechanical design is driven by the demand for higher precision and speed in these applications, and efforts to improve the effectiveness and accuracy of nanopositioning are focusing on leveraging advanced technologies and methodologies across various domains.
Let’s take a look at nanopositioning systems, first developed for research and industry applications almost 50 years ago and expected to expand in fields such as semiconductor manufacturing, optics, life sciences, and precision engineering as the technology continues to evolve.
Performance Depends On Improving Control, Sensing, And Design
Nanopositioning systems are capable of moving rapidly and maintaining consistent accuracy at the nanometer level, making them suitable for a wide range of precision applications in both research and industry. These applications include high-performance linear stages used in the production of read/write heads in computer hard drives, medical devices such as laser mirror positioning in eye surgery, live cell imaging, multi-photon microscopes used in neuroscience, and DNA sequencing. Nanopositioning systems are also used in materials research, particularly in atomic force microscopy.
The effectiveness and accuracy of nanopositioning systems depend on enhanced sensor technologies, innovative mechanical designs, and advanced control techniques, such as feedback and feedforward control, according to MDPI. These methods are crucial for managing the mechanical dynamics of nanopositioning systems, especially those using piezoelectric actuators.
Feedback control helps mitigate issues such as vibration, hysteresis, and creep, while feedforward control anticipates and compensates for these effects before they occur. Techniques such as iterative learning control and robust iterative inversion-based control have been shown to improve tracking performance and robustness in nanopositioning stages.
Force feedback control – integrating strain and force feedback in piezoelectric actuators – enhances control performance. This approach allows for high-precision tracking and vibration control, which is essential for applications requiring ultra-high precision.
Iterative learning control is a third technique. This method is particularly effective for periodic tasks, such as scanning in microscopy, by iteratively updating the feedforward input to improve tracking accuracy over time.
On to sensor technologies, starting with high-resolution position sensors with nanometer resolution that are critical for the precision of nanopositioning systems. Various sensor technologies, including capacitive, piezoelectric, and piezoresistive sensors, are employed to achieve high linearity, resolution, and speed. These sensors are essential for defining the performance metrics of nanopositioning devices.
In addition, dual-sensor arrangements – combining different types of sensors, such as piezoelectric and capacitive sensors – can improve the overall performance by compensating for the limitations of each sensor type. This approach is particularly useful in high-speed vertical positioning stages.
The third factor required for accurate nanopositioning is mechanical design. Flexure-guided systems are high-bandwidth flexure-guided systems designed to provide sub-nanometer resolution over a wide positioning bandwidth. These systems are often driven by piezoelectric stack actuators, which require careful mechanical design to avoid damage from excessive inertial forces during high-speed operations.
Microelectromechanical systems (MEMS) nanopositioners offer high precision and compact size. Innovations in MEMS design, such as self-sensing actuation and bulk piezoresistive sensors, enhance the performance and integration of these devices in various applications.
A third design factor is preload techniques which are used to protect piezoelectric actuators from damage due to inertial forces. These methods ensure that the actuators can withstand high-speed operations without compromising their structural integrity.
Nanopositioning Systems, New Technologies, And The Future
The global nanopositioning systems market is projected to grow significantly, driven by the rising demand for miniaturization of devices and components, as well as advancements in nanotechnology. According to DataHorizzon, the market is expected to reach an estimated size of $214.08 million by 2028 fueled by the increasing need for precision in various high-tech industries, including semiconductor manufacturing, biotechnology, and advanced research.
Aiding in this growth will be new technologies, including artificial intelligence (AI), according to Photonics Online. AI algorithms are being used to optimize nanoscale manufacturing processes by analyzing data from sensors and feedback systems to make real-time adjustments. This enhances the precision and efficiency of nanopositioning systems.
AI is also enabling the development of autonomous nanobots that can navigate and interact with nanoscale components to assemble complex nanostructures and devices with high precision. This innovation opens new possibilities for advanced nanodevices, sensors, and materials.
Other technological advancements playing a role in the future of nanopositioning systems are quantum computing and nanoscale electronics which, as they emerge, will drive demand for precise positioning and alignment.
The development of high-resolution sensors, such as capacitive, piezoelectric, and piezoresistive sensors, is crucial for achieving nanometer-level precision. These sensors are essential for defining the performance metrics of nanopositioning devices.
In addition, Improved calibration techniques are being developed to enhance the accuracy of nanopositioning stages. These techniques involve modeling and compensating for environmental factors such as thermal expansion and mechanical strain, which can affect the precision of nanopositioning systems.
Nanopositioning Systems Are Everywhere
Most every industry uses nanopositioning in some way. Nanopositioning is extensively used in materials research, enabling techniques like atomic force microscopy to study surface properties and nanoscale phenomena.
It is also used in semiconductor manufacturing in which nanopositioning stages are crucial in fabrication for tasks such as wafer inspection, overlay alignment, and packaging of microchips and MEMS devices. In the life sciences, nanopositioning enables high-precision manipulation and analysis in fields like genomics, single-molecule biophysics, and live-cell imaging.
Finally, nanopositioning technology is used in defense applications and infrastructure such as beam steering, satellite positioning, and controlling devices under extreme conditions such as high vacuum and cryogenic temperatures.
The effectiveness and accuracy of nanopositioning systems are being enhanced through AI integration, advanced sensor technologies, improved calibration methods, and their application across diverse industries. These advancements are essential for meeting the stringent requirements of modern nanotechnology applications and driving future innovations.