How Ultra-Fast Cameras Are Improving Automobile Crash Testing And Saving Lives

By John Oncea, Editor
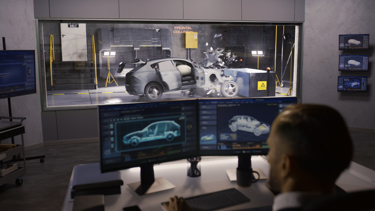
Since the 1960s, crash testing has established itself as a reliable tool for the optimization and testing of vehicle safety. Now, with the addition of high-speed cameras, crash testing is reaching new levels of proficiency.
The global high-speed camera market is booming. Valued at $3.78 billion last year, Astute Analytica is projecting it to grow to $6.39 billion by 2031. Driving that growth will be the usual suspects: technological advancements, increased demand for high-speed imaging solutions, and expanding applications across various industries.
“Key trends shaping the market,” writes Astute Analytics, “include the integration of artificial intelligence and machine learning for advanced analytics and automation, development of compact and portable high-speed cameras, and increasing demand for high-speed cameras in the sports industry for motion analysis and injury prevention.”
High-speed cameras are used by countless industries including aerospace and defense, research and development, entertainment and media, manufacturing and industrial, and sports and recreation. These cameras have a wide range of applications, including product and material testing, ballistics and explosives testing, fluid dynamics and turbulence studies, biomechanics and motion analysis, and high-speed imaging for slow-motion playback in sports and entertainment.
High-Speed Cameras In The Automobile Industry
The high-speed camera is also used in the automotive sector in various applications – such as crash tests, aerodynamics testing, and tire testing – driven by the need for safety testing and improvement. Their use in a crash test, in particular, helps capture and analyze the crash dynamics such as the deformation of the vehicle and the behavior of the occupants.
Claravision, a French company founded in 1994 that specializes in scientific and industrial imaging, notes, “Using one or more high-speed cameras is the best solution for ensuring the most accurate and reliable results. Several high-precision cameras are needed to monitor all angles and analyze all potential factors.”
One specific benefit of using high-speed cameras, according to Kron Technologies, is simplifying vibration analysis. When paired with vibration analysis software, high-speed cameras can help monitor the vibrations of machinery, preventing small issues from becoming big problems by addressing areas of stress and fatigue. Three main types of vibration analysis can be conducted with a high-speed camera and paired analysis software – frequency analysis, amplitude analysis, and phase analysis.
“Many car manufacturers use high-speed cameras to test their vehicles for crash safety testing, but vibration analysis is becoming increasingly popular. By identifying potential problems early, automotive manufacturers identify areas of concern, address them, and help reduce the incidence of recalls due to faulty construction while increasing end user safety.”
Mercedes-Benz: Putting Theory Into Practice
The Mercedes-Benz Group’s Technology Centre for Vehicle Safety in Sindelfingen (TFS) features numerous test facilities that open up new possibilities for vehicle-to-vehicle tests, the configuration of assistance systems, and the verification of vehicle concepts using alternative drive systems. Cars can be driven into each other at any imaginable angle – even automated driving maneuvers with a subsequent crash are possible. Possible collisions with differing overlap angles or side-impact tests with two moving vehicles also can be simulated.
TFS provides around 70 crash configurations including frontal crash (with varying degrees of overlap), rear impact, side impact with movable barriers and lateral post-impact, rollover test, and vehicle-to-vehicle crash.* All of these are documented by using high-speed cameras (up to 1,000 images per second), including from below utilizing glass-covered filming pits.
The pits at the collision points of the crash tracks have a depth of five meters and house modern high-speed cameras that film the impact from below. Thanks to the compact Microtrack system, the guide rails for the vehicles are much narrower than before (70 mm rather than 180 mm in the old system). This means that unlike before, almost the entire underbody of the vehicle can be filmed. The glass panels covering the pits are eleven centimeters thick and can withstand the weight of trucks, allowing for them to be tested in an enclosed hall for the first time.
Sled tests are filmed by two camera sleds moving in parallel. Mercedes-Benz developed this tandem sled procedure for filming sled tests themselves. Previously the camera was mounted on a boom which had to be accelerated and braked along with the sled, reducing the payload of the test sled. In the new system, a tandem sled fitted with cameras on each side moves in parallel with the test sled during the test. The tandem sleds are powered by linear electric motors.
* The side markings along the crash tracks, which look like a QR code, are there to provide orientation to a drone that flies along the track before a crash to make sure that there are no longer any personnel there. Not necessarily high-speed camera related but yeah, cool.
A Bright Future
The increasing growth of the use of high-speed cameras in automobile crash testing is going to require equipment that offers faster speeds, higher resolution, and enough ruggedness to withstand the high G-forces produced during the test. These cameras also need to be easily networked as multiple views of the tests are needed.
As companies continue to refine their high-speed cameras to meet these requirements, their ability to provide high-quality and precise data is going to continue to drive the market and keep the technology relevant despite the availability of alternative technologies.