How To Select The Best Optical Adhesive For Your Application
By Barry Siroka, EpoxySet
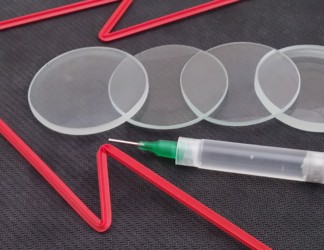
Choosing the best adhesive for a specific application can be complex. There are many application and performance needs, not to mention numerous types of adhesive chemistries with their own set of unique capabilities. Assuming a certain adhesive meets your needs could prove costly in both time and money. But asking a few questions before you make your decision could greatly reduce the number of products to be evaluated and increase the likelihood of success.
Consider the following parameters as you prepare to make your purchase:
- Substrates. Optical components are made of a wide variety of glasses and plastics. However, the term “plastic” is generic, so knowing the exact substrate is essential for determining the correct adhesive. For example, ABS and Teflon are both plastics but Teflon requires an acid etch to achieve a bond where ABS can usually be bonded with just an alcohol cleaning. Additionally, some substrates are difficult to wet on a molecular level, so specific adhesive chemistries may be required. Many optical component surfaces are also coated, and the coating may present bonding concerns.
- Cleanliness of the parts. Most adhesives require that the substrates be prepared properly. Will it require a simple cleaning or a more complex operation, such as abrasion, chemical etch, or plasma treatment?
- Viscosity. Low viscosity (thin) products are best for thin bonds or for applications requiring wicking. Thixotropic materials (won’t run) are best for use in vertical applications.
- Thermal cure vs. UV cure. UV cure adhesives are usually one part and can be cured quickly. Most UV cure adhesives must also be exposed directly to UV energy to cure, so at least one of the substrates must allow transmission of UV. Thermal cure materials can be cured at room temperature and/or with heat. Heat-cured thermal adhesives might require high temperatures, which could be detrimental to components but, in general, will cure faster with higher properties.
- Working life. Working life is the length of time you can apply a two-part adhesive before it gels. Remember that working life is generally related to cure time. For thermal cure materials, a longer working life usually means a longer time to fully cure (at room temperature). Single-part UV cure materials can be cured quickly, and the working life concept doesn’t apply.
- Configuration. Especially true for small optical components, the dimensions of the parts and how they fit together are very important to determining the best material. Certain adhesives are designed to work best with thin bond gaps and may not work in thicker gaps. Larger parts and thicker bond gaps may require a slower cure to reduce shrinkage.
- Required performance. Consider how you want the adhesive to perform and under what conditions. Here are some questions to ask before selecting an adhesive:
Does the adhesive need to form a structural bond?
Ideally, a structural bonding material will create a finished part that is as strong as the substrates. As stated earlier, knowledge of the composition of the substrates helps to decide the best adhesive and preparation to accomplish an ultimate bond. Also, understanding the configuration of the parts to be bonded will determine the types of adhesives for use. With most adhesives, the larger the surface area of the mated parts, the stronger the bond.
Again, the bond gap is also critical. Various adhesive chemistries work best with certain gaps. In general, cyanoacrylates and anaerobics need the thinnest bond line, where epoxies and urethanes are better with thicker gaps.
How much stress will the bond endure?
The forces on the adhesive joint and the direction of those forces have a major role in the adhesive to be used. Some chemistries may have excellent tensile strength (strength in a horizontal direction) and very little shear strength (strength in a vertical direction). Compressive forces or torsion on the joint should also be considered; adhesives may be formulated to be more flexible or with fillers to compensate for these stresses.
Will any stresses be consistent or intermittent?
Some adhesives can take extreme stresses for very short periods but not withstand stress over long periods. Others may hold up to long, consistent stress but not to stress brought on suddenly.
What optical properties are important?
If light transmission is important, we must know the wavelength being transmitted and the duration. Optical adhesives may only transmit in specific wavelength ranges. For example, most UV-curing adhesives will not transmit below 400nm. You may also need to consider the refractive index of the substrates. Lastly, certain chemistries will not remain clear over long exposure to UV radiation.
What are the temperature requirements during processing and use?
Materials with low temperature cures may not withstand high temperatures during use. Adhesives designed for high temperature uses might only cure with heat, so the adhesive will have to be exposed to dry heat (an oven or a heat element).
Consider exposure temperatures and whether parts will be temperature cycled. Many materials that withstand high temperatures will crack when cycled to low temperatures, and low temperature materials might lose their strength at high temperatures.
Does the cosmetic appearance matter?
Some adhesive chemistries can be easily colored but others cannot. Some chemistries will have lot-to-lot variations and therefore the final appearances may differ. In applications requiring specific colors (especially for consumer products), it may be necessary to ensure that lots can be color matched.
Will there be any excessive humidity during use or testing?
Most adhesives will not withstand high humidity at high temperatures.
Asking the right questions and knowing as many answers as possible is crucial to selecting the best optical adhesive for your application. While it is not always feasible to know all the required parameters, it is important to have as much information as possible to make an educated decision. But perhaps more important to know is that there is no substitute for sampling and evaluating a product. Testing adhesives before widespread or final use can reveal previously unconsidered parameters.
About The Author
Barry Siroka has over 42 years’ experience in adhesive and specialty polymers, beginning his career in technical support for W.R. Grace (Emerson & Cuming) before joining National Starch (Tra-Con) where he eventually rose to vice president. After 11 years of customer service, technical training, and marketing, Siroka transitioned to become head of Business Development at Fiber Optic Center. He has been with EpoxySet for 7 years, where his formal chemistry education and technical expertise help facilitate users’ optical adhesive selections.