Enabling Low-Cost Production Of 3D Nanostructures
By Chuck Seegert, Ph.D.
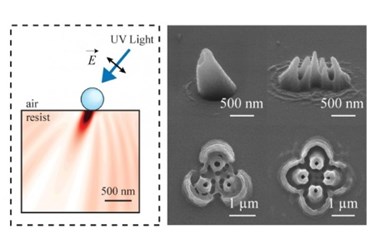
Researchers from North Carolina State University have developed a new lithographic method that creates 3D nanostructures using nanospheres instead of more expensive, conventional methods. The technique eliminates the stacking of 2D patterns in the production of 3D structures and could find application in the biomedical, electronic, and photonic space.
In the field of lithography, creating intricate 2D patterns is a difficult task, and many methods and techniques have been developed to make it more reliable and effective. Lasers can be used in conjunction with specialized lenses to create nanoscale 2D patterns on a photosensitive surface. To create 3D features, many 2D patterns are printed on top of each other, which makes the process more complex. While these methods have been successful, the equipment necessary to perform lithographic pattern generation is extremely expensive.
A new low-cost method from North Carolina State University (NCSU), however, may enable nanoscale “inkjet printers” that can print biological structures, electronics, antennas, and even photonic components, according to a recent article from NC State News. To achieve this, the team used transparent nanospheres when exposing photosensitive layers to light. The bending and scattering of light by the nanospheres led to predictable patterns that were cast onto to the photosensitive layers, leading to the development of unique 3D structures.
Where other techniques require stacks of 2D layers to create 3D structures, the new method can create geometries by manipulating variables in the exposure technique, according to the press release. The size of the nanosphere along with the angle, wavelength, and polarization of the light can all contribute to the geometry of the final structure. Using self-assembly methods, the nanospheres can even be placed in regular arrays so the resulting 3D nanostructures will be uniformly organized.
“This could be used to create an array of nanoneedles for use in drug delivery or other applications,” said Xu Zhang, an NC State Ph.D. student who contributed to the work, according to NC State News.
How the light interacts with the polystyrene nanoparticles is key to how these patterns are created, according to a recent paper published by the team in the journal Small. Oblique illuminations on the nanospheres lead to intensity distributions that, when processed, provide hollow-core nanostructures. In some cases, using multiple light sources allows the photoresistive layer to be sculpted into other unique 3D features. The hollow-core designs are low-cost and have the potential for high throughput in manufacturing.
Attempts to find low-cost nanoscale manufacturing methods is a goal of many research groups. Recently, in an article published on Med Device Online, a nanomotor lithography method was discussed that also used low-cost, alternative manufacturing methods.
Image Credit: Xu Zhang